How Are Carpets Made?
Carpets add warmth, comfort, and value to a home. But have you ever wondered—how exactly are they made?
There are seven major steps in carpet making:
Fiber creation
Yarn preparation
Tufting
Dye application
Secondary backing
Finishing
Quality control
The method used to make carpets affects their quality and durability and acts as a determining factor in choosing the proper cleaning or vacuuming method.
Our focus today is the process of carpet making, where they're made, and how to distinguish a handmade carpet from a machine-made carpet.
Read on.
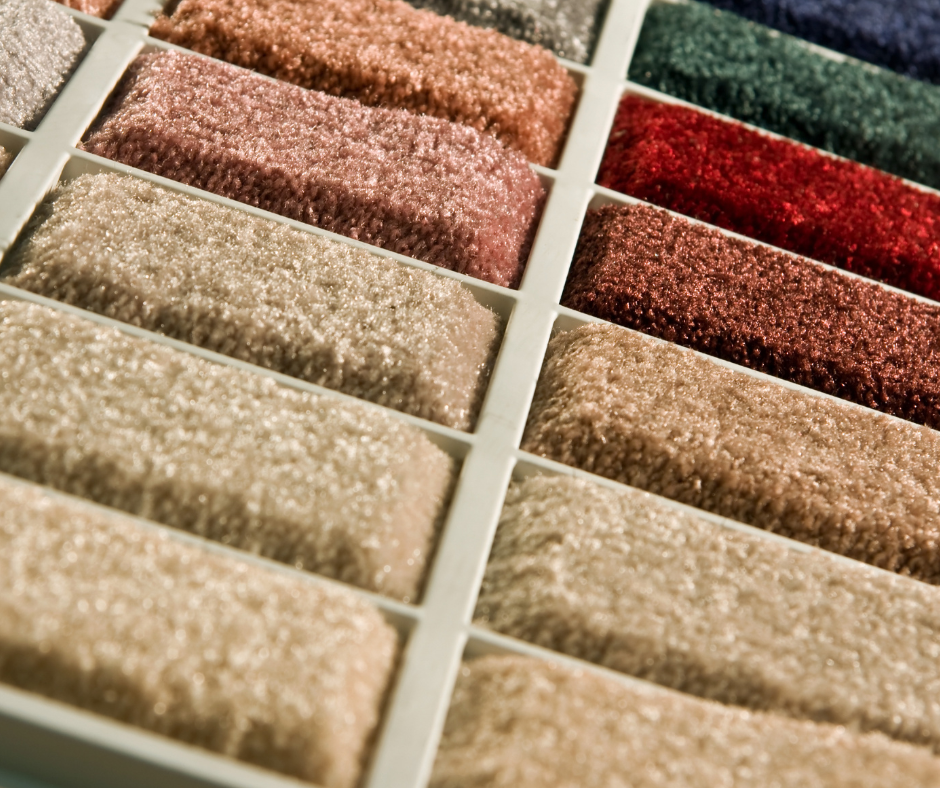
Where Are Carpets Made?
Many carpet manufacturing companies exist globally, but two stand out: Shaw Industries Group, Inc. and Mohawk!
Shaw
Shaw is based in Dalton, Georgia. After the death of J.C Shaw's and Robert Shaw's father, the two brothers acquired the Philadelphia Carpet Company in 1967. They retooled the Philadelphia Carpet Company for carpet manufacturing and rebranded it to Shaw Industries Group, Inc. The company went live in 1971.
In 1972, the company wanted to process filament nylon yarn continuously; it bought a spinner of fine-gauge carpet yarns to start heat-set and twisting operations.
In 1982, the company's CEO, Robert Shaw, started selling directly to retailers, thus opening more regional warehouses across the United States. The move skyrocketed the company's sales, making it the largest carpet manufacturer in the United States.
According to gpb.org, Shaw is the Carpet Capital of America, producing 75 percent of the world's rugs and carpets.
Only 25 percent of the world's carpet comes from other companies, making Shaw Industries Group, Inc. the leading and largest carpet manufacturer globally.
Mohawk
After several years of moving to the United States in 1875, William Shuttleworth and his sons started a carpet mill. After William's death, his four sons relocated to the company in 1902, and it became a corporation called Shuttleworth Brothers Company.
In 1920, the company took on a new name: Mohawk Carpet Mills, Inc. During this time, it also acquired Wallin, Crouse, and McCleary.
During the Second World War (WWII), America was undergoing a Great Depression. Wool became more scarce, and its price shot up, making it hard for average families to afford woolen carpets between 1900 and 1960.
Due to the scarce supply and high wool prices, Mohawk Carpet Mills, INC. founders started looking for more affordable fibers after WWII. They found man-made synthetic fibers such as acrylic and nylon more consistent and affordable even to the average earner.
In the late 1940s and 1950s, Mohawk Industries, Inc. adopted tufting to enable the production of broadloom carpets.
In 1980, David Kolb became the CEO. He moved the company to Atlanta, GA, and eliminated the middleman. By 1990, the industry had moved to second place in carpet production globally.
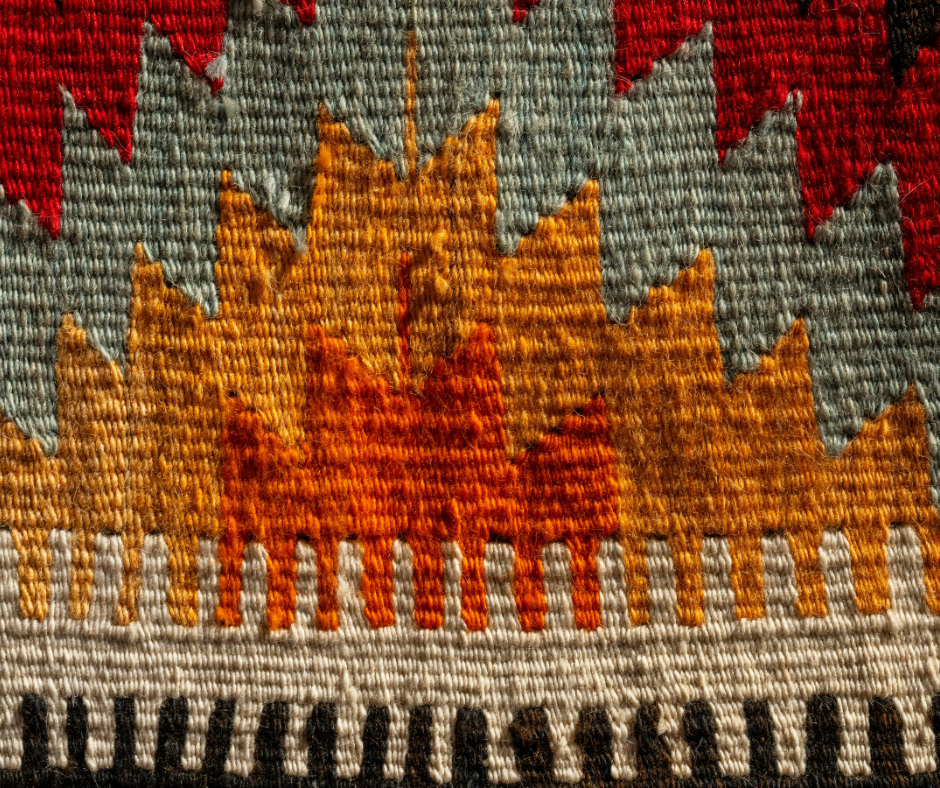
How Are Carpets Made?
The method used to make a carpet determines its durability, comfort, and eco-friendliness. The method also determines how to clean a carpet, its ability to wear evenly, and its performance.
What is the process of making a carpet?
Fiber Creation
Most carpets are made from wool, nylon, Olefin, and polyester fibers. Synthetic fibers are produced using chemical processes, while natural fibers, such as cotton and wool carpets, are sourced from plants and sheep, respectively.
Yarn Preparation
Fibers are spun to produce yarn, then treated or twisted to make it durable and stronger. Yarns are thicker than fibers and thus suitable for carpet making.
Tufting
A tufting machine featuring hundreds of needles pushes yarn through the carpet backing, creating loops of yarn. A sharp blade cuts the loops to create a plusher surface. Carpets made of cut loops are cut pile carpets, while the uncut loops create loop pile carpets.
Dye Application
The next step is deck dyeing, which is dying large batches of carpets. Dye application during production can be done using more complex machines that inject multiple colors along the carpet.
Secondary Backing
At this stage, a secondary backing layer is applied to the tufted carpet, helping to maintain its shape and increase its stability.
Finishing
The carpet finishing process may involve applying stain protection, trimming the pile height (shearing), and steaming to improve quality.
Quality Control
Quality checks ensure that the carpet meets the required quality level in terms of durability, color, and pile consistency, among other things.
How Handmade Carpets Are Made?
There are 6 steps involved in making handmade carpets:
Processing the Fiber Into Yarn
Carpet fibers undergo processing to turn them into yarn to make carpets. Different fibers undergo different processing methods. Wool fibers, for example, undergo scouring to remove grease and other contaminants.
An apparatus pulls the fibers into individual strands, which are spun into yarn using a traditional spinning wheel.
Washing the Yarn
The next step is washing the yarn to remove dust, grease, or other foreign substances, depending on the type of yarn you're working with.
The process of washing may vary depending on the type of yarn. The yarns are immersed in a detergent bath, scrunched several times, and then rinsed in clean water to remove the detergents.
The clean yarn is dried under the sun for several days based on the weather.
Yarn Dying
The dye is made from synthetic and natural elements, giving a great hue. The clean yarn is submerged in a dye and heated to boiling temperatures for a certain duration.
Yarn that undergoes boiling for a longer time has a darker hue, and the dye is permanent; thus, it doesn't fade or bleed when cleaning the carpets.
After dying, the yarn is exposed to the sun to dry completely to make carpets.
Handweaving the Yarn
There are three ways of making hand-woven carpets: hooking, knotting, or tufting. Tufting, the most common method, involves using stencils to draw a pattern in the chief backing material.
The weaver uses a tufting gun to insert tufts of wool into the chief backing, covering it with latex. The weaver adds a secondary backing material, resulting in a loop pile. After cutting the pile, the result is a flat surface featuring a dense pile.
Hooking is the most affordable and easiest way of making hand-woven carpets. In the knotting (hand-tying) method, an artisan draws a unique design on graph paper. A weaver then vertically stretches down columns of thread to create a frame and starts weaving the yarn knot-by-knot using a Persian knot, Turkish knot, Tibetan knot, or other traditional method. This process of weaving is particularly common in making wool carpets.
In the hooking method, the weaver chooses the colors, design, and patterns (mostly) from pictures or other carpets.
An artisan lowers or raises the position of the carpet's length using a scaffolding system. Using a specialized tool, the artisan pushes the carpet yarns forth and back along the carpet backing.
Carpet Washing and Drying
After placing the carpet on a flat surface, the manufacturer pours water to clean it, removing yarn motes, dirt, and detergent.
Wood planks featuring sharp edges help to force water out of the carpet.
Quality Inspection
Carpets must undergo quality inspection before selling.
Carpet quality grading differs depending on the country of manufacture and the type of carpet.
Carpet grading in other countries except China is based on Knots Per Square Inch (KPSI), a key measure of durability, quality, and value of hand-knotted carpets.
Carpets with more knots are more expensive and have a higher design clarity and complexity.
Below is a table showing carpet quality grading based on the Knots Per Square Inch.
Knots Per Square Inch (KPSI) |
Carpet Grading |
290 and above |
Extremely Fine |
160 - 290 |
Very Fine |
130 - 160 |
Fine |
60 - 130 |
Medium Fine |
30 - 60 |
Coarse |
30 |
Very Coarse |
Handmade carpets are more durable and feature different textures and patterns. They're more expensive due to the labor involved in their production.
Handmade carpets have a better feel and appearance and are thicker than machine-made carpets. Various handmade carpet textures and designs make choosing a more personalized carpet easier.
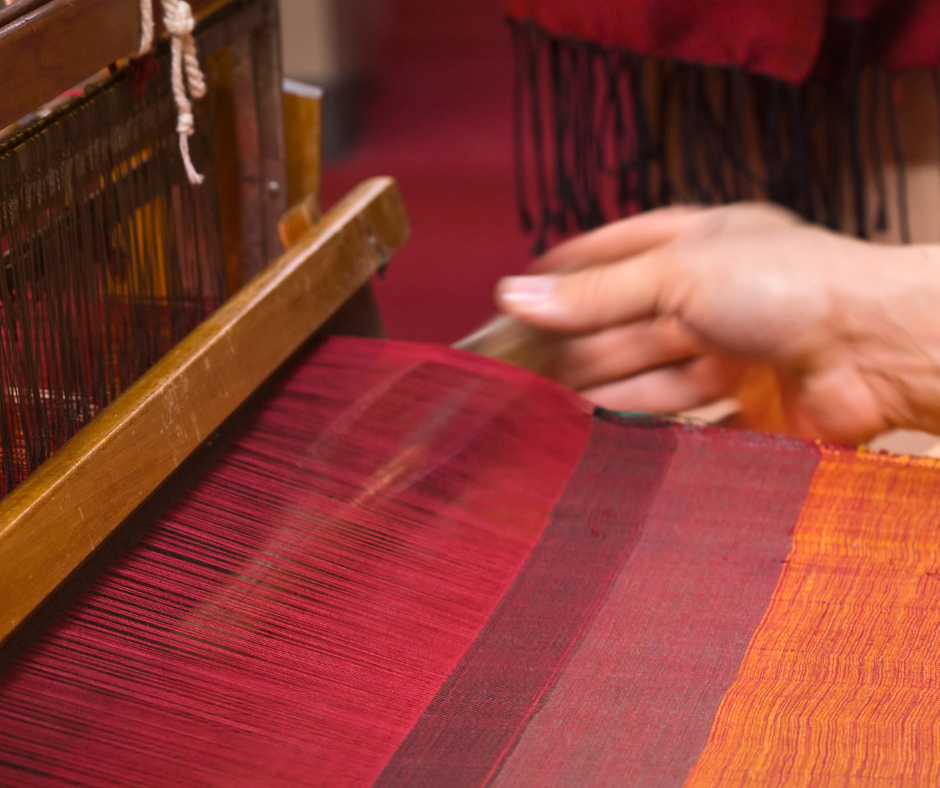
How Can You Tell if a Carpet Is Handmade?
Handmade carpets are made by human hands by handweaving, hand knotting, or hand tufting. Based on their design, complexity, and size, they take more time (weeks or months) to make than machine-made carpets, making them more expensive.
Handmade carpets are a preference due to their uniqueness, artistry, and durability.
You can know if a carpet is handmade by looking at the factors related to its material and construction, such as unevenness and fringes.
Unevenness/irregularities: Handmade carpet irregularities include design, weaving, and pile unevenness. Some easy-to-notice irregularities involve subtle imperfections, knot density, and slight asymmetry design. Machine-made carpets feature even patterns.
Fridges: If you notice hand-tied fridges on the back of the carpet, that's a sign it's handmade. Fridges (extending threads) are a carpet's foundation extension. The fridges have visible knots at the base since they're handmade (manually knitted) and are slightly uneven in thickness and length. Machine-made carpets don't have extending fringes.
How Are Car Carpets Made?
Molded carpets are the carpets used in cars' interiors. A molded carpet must firmly hug the car's floor plans to eliminate chances of loose fitting or pockets after carpet installation. There's a backing that prevents pockets in between the floorplans and the carpet.
The steps below show the car carpet-making process.
Designing: Carpet design mimics the car's design and parameters. Some cars have unique designs, requiring precise carpet sizing.
Cutting plastic sheets: A precise knife cuts a sheet of polymer, rubber, or textile into the desired design. These sheets act as the base layer.
Pattern cutting: Edges preparation and cutting out of the patterns are done in advance to ensure they align perfectly with the main part of the car carpet. Proper edge positioning protects the base material against mechanical damage and stretching.
Installation of specialized fixings: Specialized fixings keep the product in a certain location or position. Proper machinery helps fasten the fixings, such as universal eyelets, Velcro, and mounting hooks or elements integrated with the floor.
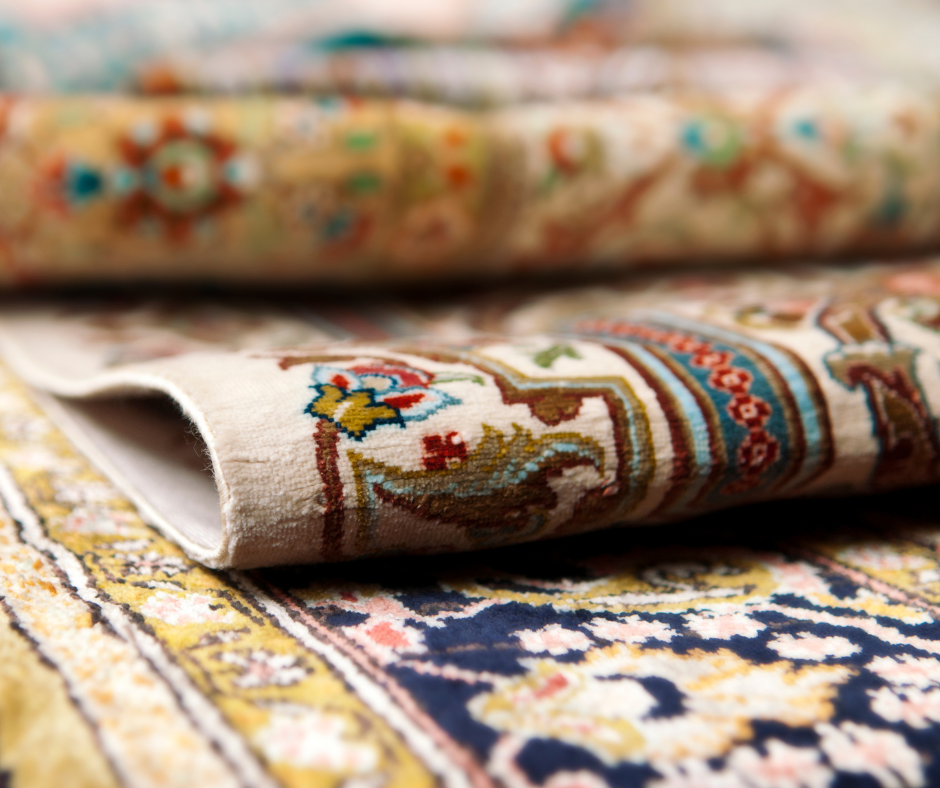
How Are Carpet Fibers Made?
Understanding the process of making carpet fibers is crucial; it helps to know what carpets to avoid if you're allergic or concerned about the toxins the carpet may release into your indoor air.
The most common carpet fibers are wool, jute, nylon, and Polyester; each type of fiber undergoes a different processing method.
Nylon
Nylon fibers undergo a process called extrusion, which involves melting polymer chips. The viscous, thick liquid is pushed through the holes of a spinneret (spinnerette) to form continued filaments of semi-solid polymer.
Spinnerets may feature one or hundreds of holes. After the liquid polymer converts into a rubbery state, it solidifies. The next process is spinning (not the same process as spinning fibers to make yarns), which helps solidify and extrude continuous filaments.
The nylon fibers are held together and then twisted into a continuous bundle. Later, exposure to cooling air hardens the nylon fiber strands, making them a single filament.
The hardened strands are stretched to a smaller diameter and then twisted and wound around a bobbin.
Filament drawing during or after the hardening of the extruded fibers helps to increase their strength. Combining the molecular chains and their positioning along the nylon fiber axis results in a stronger, durable nylon yarn.
Synthetic fibers are produced in the bulked continuous filament (BCF) and are used in staple form (later spun into yarn), cut-pile, and loop-pile carpets.
Fiber extrusion occurs in varying cross-sectional shapes such as octagonal, round, pentagonal, and trilobal.
The original nylon fibers were round, magnifying the soil in the carpets. Adding delustering dulled the colors, but the soil magnification was less in the nylon carpets.
The magnification of soil in trilobal carpet fibers is much less. This shape scatters more light, giving the fibers an attractive sparkle while lessening soil visibility.
Hollow and pentagonal-shaped nylon carpet fibers reveal less dirt and soil, making them a great choice for high-traffic places. Hollow nylon carpet fibers offer better thermal insulation. Octagonal nylon fibers are glitter-free.
Jute
Jute, a natural fiber, is spun from the skin of flowering shrubs in the mallow family Malvaceae and genus Corchorus. The fibers undergo several steps to make them ready for weaving.
Below are the steps for making jute carpet fibers.
Fiber Harvesting: Farmers put several bundles of stalks in water for 20 days after jute harvesting.
Separating and removing impurities: After 20 days, the fibers are separated from the stalks, resulting in long and thin strands. The manufacturers wash the strands under running water to eliminate impurities and other extraneous matter.
Carding: Manufacturers run the fibers through the carding machine, which splits the fibers to remove the inner extraneous materials. This process also arranges the fibers into ribbon-like structures (sliver).
Drawing: Manufacturers mix the slivers using drawing machines to increase fiber strength and reduce sliver thickness and width. They can repeat the process several times to strengthen the fiber further.
Combing: The manufacturers comb the slivers to create smooth, fine fibers and improve their alignment.
Spinning: Manufacturers stretch and twist slivers into jute yarn using a spinning machine. Tightly winding jute slivers together result in durable and strong fibers.
Winding: The last process uses a spooling machine to wind the yarns into spools for carpet making.
Wool
Special sheep breeds produce wool suitable for carpeting. These breeds produce coarse, thick fleeces suitable for carpeting. Below is the process of making wool fibers for carpets, from shearing to spinning.
Shearing
Sheep shearing helps to remove the fleece and skirting. This process removes the unwanted (too dirty to clean) parts from the fleece. Some of the unwanted bits include poop and vegetable matter such as seeds, hay, and burrs.
Raw Wool Scouring
Raw wool has grease and other contaminants, such as dust, sand, and dirt; scouring removes them. Fleece goes through a series of bowls, sometimes up to 8, which contain washing liquid to remove contaminants.
The first two or three bowls have warm water and detergent to remove emulsified or water-soluble compounds. These initial bowls may sometimes have an alkali.
The rest of the bowls have fresh water to rinse the wool and remove washing detergents and chemicals.
The wool later passes through a continuous dryer to remove excess water. Next, the clean wool passes through several machines, where it undergoes mechanical beating to remove water-insoluble compounds such as dust and sand.
The key thing during scouring is to ensure minimal fiber felting or entanglement, which causes excessive fiber breakage in later manufacturing stages. This could affect the carpet quality and wear performance.
Blending
The next step is separating fiber groups into small pieces. After pneumatically transporting the loose wool into a bin (closed room), manufacturers mix it with other fibers, such as nylon. The manufacturer later stands it in the room to condition it until the moisture content stabilizes.
Carding
Wool is run through tiny metal rods to disentangle and tease out the strands. This transforms them into firmer, more consistent material, later divided into small strips called wool pencil roving.
Spinning
Manufacturers transfer roving from the rolls to smaller spools, which they twist into yarns. They can twist several wool strands to create a heavier, thicker yarn. Several strands make a ply; for example, two- and three-ply yarns are made of two and three smaller strands, respectively.
A two- or three-ply yarn makes strong wool carpets that resist flattening and wear.
Dying
To help the dye set permanently in the wool fibers, vats of dye are mixed with water and heated to high temperatures. Woolen fibers are dyed using acidic dyes to ensure the dye bonds with the fibers at a chemical level to prevent color bleeding.
Drying
Wool yarn drying occurs on-screen tables where hot air is circulating or on sheets set in the sun to dry evenly and adequately.
Zerorez Offers Professional Cleaning Services for All Types of Carpets (and Floors)!
Professional carpet cleaning services are essential to remove dirt, debris, stains, oils, and dust from carpets, extending their longevity and maintaining their aesthetic.
Our team has exceptional experience cleaning all types of carpets (and floors).
We're only a call away, but you can also schedule a carpet cleaning service.
We usually apply premium fiber protectors (on demand and at an extra cost) to keep your carpets cleaner longer, saving you money and time.
Call us, and let's transform your home in a few hours or days if you need whole-house cleaning services.
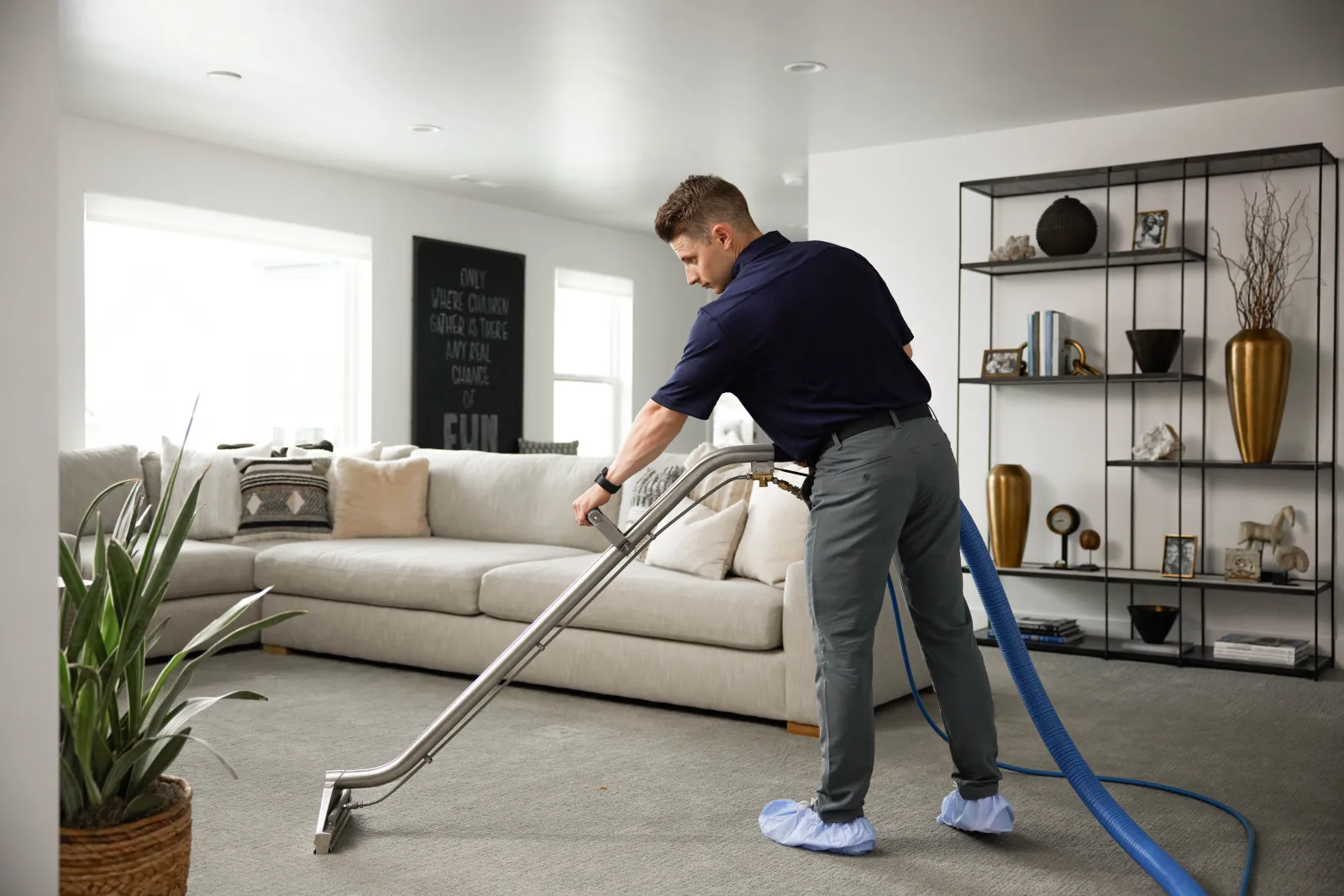